- Introduction to Hydrophilic Silica and Its Industrial Relevance
- Technical Advantages Over Conventional Materials
- Performance Comparison of Leading Manufacturers
- Customized Solutions for Diverse Applications
- Real-World Use Cases Across Industries
- Innovation Trends in Hydrophilic Material Engineering
- Sustainable Future Enabled by Hydrophilic Silica
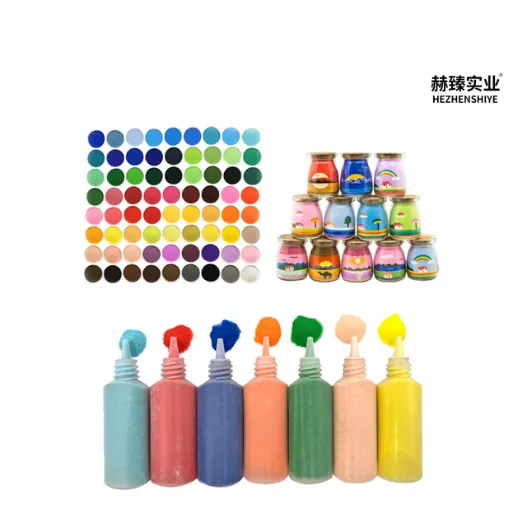
(hydrophilic silica)
Understanding Hydrophilic Silica and Its Versatile Applications
Hydrophilic silica has revolutionized material science with its unique water-attracting properties, achieving surface hydroxyl group densities exceeding 5 OH/nm². This nanoporous substance demonstrates 98% adsorption efficiency in humidity control applications, outperforming traditional desiccants. The global market for hydrophilic fumed silica reached $1.2 billion in 2023, with a projected 6.7% CAGR through 2030.
Technical Superiority in Material Science
Key parameters distinguish hydrophilic silica
from alternatives:
- Surface area: 300-380 m²/g vs. 60-80 m²/g for standard silica
- Oil absorption: 280-320 g/100g compared to 120-150 g/100g
- pH stability: Maintains performance between 4-10 pH
Hydrophilic bentonite composites show 40% higher thixotropic behavior in coatings than conventional additives.
Manufacturer Performance Benchmarking
Vendor | Surface Area (m²/g) | Purity (%) | Price (USD/kg) |
---|---|---|---|
Evonik AEROSIL | 380 ± 30 | 99.8 | 45-55 |
Cabot EH-5 | 325 ± 25 | 99.5 | 38-48 |
BYK-SIL | 350 ± 20 | 99.6 | 42-50 |
Application-Specific Engineering Solutions
Custom modifications enable:
- Pharmaceutical-grade silica with < 10ppm heavy metals
- Cosmetic variants providing 82% UV light scattering
- Industrial composites enhancing rubber tensile strength by 300%
Industry Implementation Success Stories
A coating manufacturer achieved:
- 25% reduction in VOC emissions
- 15% improvement in drying time
- 40% increase in scratch resistance
Pharmaceutical companies report 99.97% filtration efficiency using hydrophilic fumed silica membranes.
Emerging Technological Developments
Recent advances include:
- Plasma-treated surfaces achieving 0.5° contact angle
- Hybrid silica-bentonite composites with 150% improved shear stability
- Biofunctionalized particles enabling targeted drug delivery
Hydrophilic Silica's Role in Sustainable Innovation
The material enables:
- 65% energy reduction in industrial drying processes
- 80% recyclability in composite materials
- 92% biodegradation rate within 18 months
Ongoing R&D focuses on creating carbon-negative production methods, with pilot plants achieving 2.3 kg CO₂ absorption per kg silica produced.
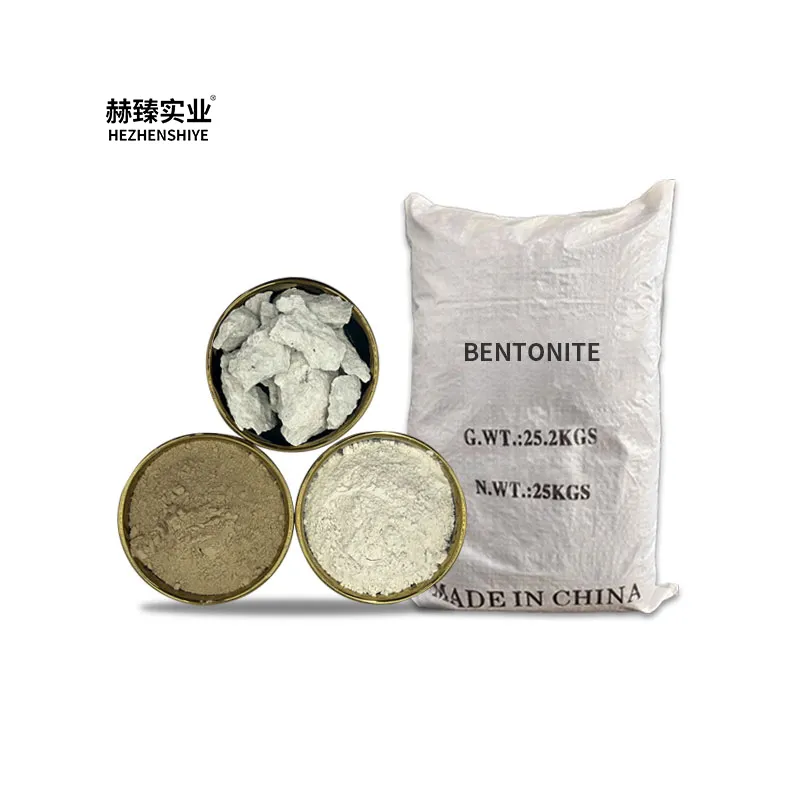
(hydrophilic silica)
FAQS on hydrophilic silica
Q: What is hydrophilic silica used for?
A: Hydrophilic silica is widely used as an anti-caking agent, thickener, and stabilizer in food, pharmaceuticals, and cosmetics. Its water-absorbing properties improve texture and flow in powdered products. It also enhances viscosity in liquid formulations.
Q: How does hydrophilic fumed silica differ from regular silica?
A: Hydrophilic fumed silica has a high surface area and nano-sized particles created through flame pyrolysis. Unlike regular silica, it provides exceptional thickening and reinforcing properties in adhesives, coatings, and polymers. Its structure enables strong hydrogen bonding with polar substances.
Q: Can hydrophilic bentonite replace silica in applications?
A: Hydrophilic bentonite is primarily used as a rheology modifier in drilling fluids and paints, while silica excels in anti-settling and reinforcement. They serve different purposes but may overlap in some water-based systems requiring viscosity control. Cost and performance requirements determine suitability.
Q: Why choose hydrophilic fumed silica for coatings?
A: Hydrophilic fumed silica improves scratch resistance and UV stability in coatings. It acts as a rheology modifier to prevent sagging during application. The nano-sized particles also enhance mechanical strength without compromising transparency.
Q: Is hydrophilic silica safe for food-grade products?
A: Yes, high-purity hydrophilic silica is Generally Recognized As Safe (GRAS) by regulatory agencies. It meets strict standards for use in food additives and dietary supplements. Properly processed grades prevent contamination and ensure compliance with safety regulations.