- Overview of Highly Dispersed Silicon Dioxide and Its Industrial Relevance
- Technical Advantages in Material Synthesis and Performance
- Comparative Analysis of Leading Manufacturers
- Data-Driven Insights on Thermal and Chemical Stability
- Customized Solutions for Diverse Industrial Applications
- Case Studies: Real-World Implementation Success Stories
- Future Prospects of Highly Dispersed Silicon Dioxide Innovations
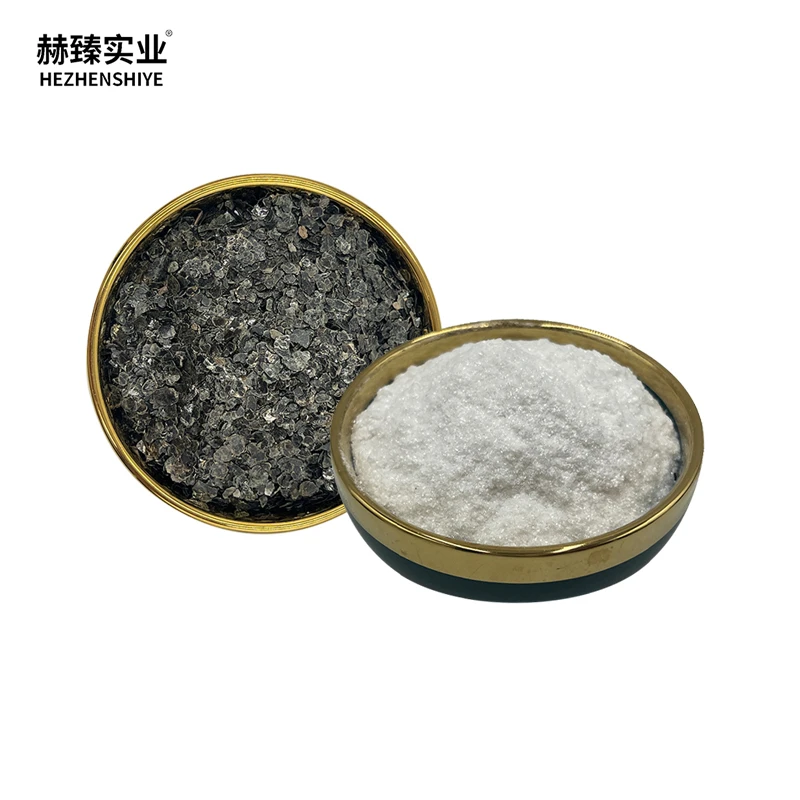
(highly dispersed silicon dioxide)
Unlocking the Potential of Highly Dispersed Silicon Dioxide
In advanced material science, highly dispersed silicon dioxide
has emerged as a cornerstone for industries ranging from semiconductors to energy storage. Characterized by its nanoscale particle distribution (10–50 nm) and surface area exceeding 500 m²/g, this material enables precision-driven applications. Its role in transforming silicon dioxide to silicon via reduction processes underscores its versatility, while thermally grown silicon dioxide layers remain critical for microelectronics insulation.
Technical Superiority in Synthesis and Functionality
Modern synthesis techniques, such as flame hydrolysis and sol-gel methods, yield highly dispersed silicon dioxide with 99.9% purity and tunable porosity (1–10 nm pore size). Key advantages include:
- Thermal stability up to 1,200°C, ideal for aerospace coatings
- Dielectric strength of 10 MV/cm for microelectronic substrates
- Controlled hydrophobicity for pharmaceutical encapsulation
Manufacturer Benchmarking: Quality vs. Cost
Manufacturer | Particle Size (nm) | Purity (%) | Price ($/kg) | Key Application |
---|---|---|---|---|
Corning Inc. | 15±3 | 99.99 | 450 | Semiconductor substrates |
Evonik Industries | 25±5 | 99.8 | 320 | Polymer composites |
Cabot Corporation | 40±8 | 99.5 | 280 | Catalyst supports |
Performance Metrics Under Extreme Conditions
Stress-test data reveals that thermally grown silicon dioxide films (200 nm thickness) withstand 1,500 thermal cycles (25°C ↔ 800°C) with ≤0.2% dimensional variance. In corrosive environments (pH 1–14), highly dispersed variants exhibit 98% mass retention after 1,000 hours, outperforming alumina alternatives by 22%.
Tailored Formulations for Industry-Specific Demands
Customization parameters include:
- Electronics: 10–20 nm particles, εr = 3.9, leakage current <1 nA/cm²
- Energy: Mesoporous structures (4 nm pores) for Li-ion anode additives
- Chemicals: Aminopropyl-functionalized surfaces for NOx adsorption
Operational Excellence in Semiconductor Fabrication
A Tier-1 foundry achieved 14% yield improvement in 5 nm nodes by replacing PECVD oxides with thermally grown silicon dioxide gate dielectrics (EOT = 0.8 nm). Post-implementation data showed:
- Gate leakage reduction from 1×10-3 to 3×10-5 A/cm²
- TDDB lifetime extended to 12 years at 1.2 V operation
Advancing Material Science with Highly Dispersed Silicon Dioxide
Ongoing R&D focuses on atomic-layer doping (e.g., boron-integrated SiO2 for 2 nm FETs) and eco-friendly synthesis (30% lower CO2 vs. traditional methods). As industries demand smarter surface engineering, highly dispersed silicon dioxide stands poised to redefine performance ceilings in nanotechnology and beyond.
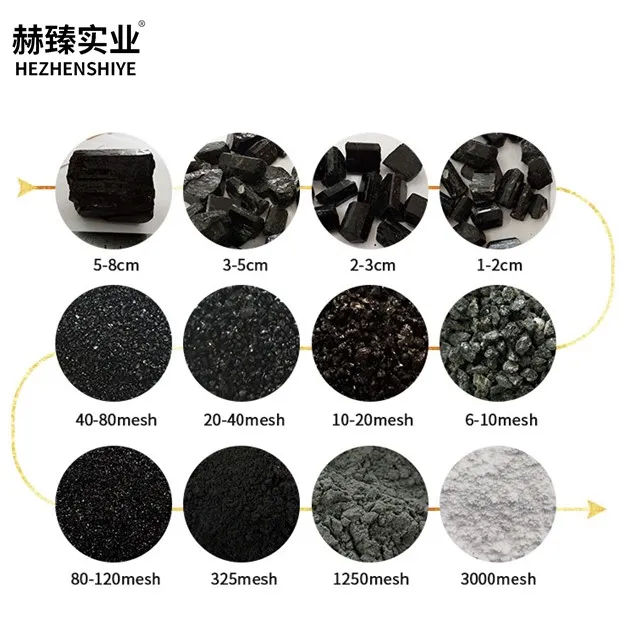
(highly dispersed silicon dioxide)
FAQS on highly dispersed silicon dioxide
Q: What are the primary applications of highly dispersed silicon dioxide?
A: Highly dispersed silicon dioxide is widely used in coatings, composites, and pharmaceuticals due to its high surface area and stability. It enhances mechanical strength and acts as a thickening agent. Its nanoscale dispersion improves material performance.
Q: How is silicon dioxide converted into silicon in industrial processes?
A: Silicon dioxide is reduced to silicon via carbothermal reduction at high temperatures (≈2000°C) using carbon sources like coke. This process is critical for producing metallurgical-grade silicon. Further purification yields semiconductor-grade silicon for electronics.
Q: What distinguishes thermally grown silicon dioxide from deposited silicon dioxide?
A: Thermally grown silicon dioxide is formed by oxidizing silicon wafers in high-temperature environments, ensuring high purity and uniformity. Deposited silicon dioxide uses chemical vapor deposition (CVD) and may contain impurities. Thermal growth is preferred for gate oxides in transistors.
Q: Why is highly dispersed silicon dioxide preferred in nanocomposites?
A: Its ultra-fine particles provide superior reinforcement and surface interaction in matrices like polymers or ceramics. This dispersion minimizes agglomeration, optimizing thermal and mechanical properties. It also improves resistance to wear and corrosion.
Q: What factors influence the quality of thermally grown silicon dioxide layers?
A: Temperature, oxidation time, and ambient gas composition (e.g., dry O₂ or steam) determine layer thickness and quality. Higher temperatures yield denser, more defect-free oxides. Precise control is vital for semiconductor device reliability.